Abstract
The additive manufacturing (AM) process metal powder bed fusion (PBF) can quickly produce complex parts with mechanical properties comparable to that of wrought materials. However, thermal stress accumulated during Metal PBF may induce part distortion and even cause failure of the entire process. This manuscript is the second part of two companion manuscripts that collectively present a part-scale simulation method for fast prediction of thermal distortion in Metal PBF. The first part provides a fast prediction of the temperature history in the part via a thermal circuit network (TCN) model. This second part uses the temperature history from the TCN to inform a model of thermal distortion using a quasi-static thermo-mechanical model (QTM). The QTM model distinguished two periods of Metal PBF, the thermal loading period and the stress relaxation period. In the thermal loading period, the layer-by-layer build cycles of Metal PBF are simulated, and the thermal stress accumulated in the build process is predicted. In the stress relaxation period, the removal of parts from the substrate is simulated, and the off-substrate part distortion and residual stress are predicted. Validation of part distortion predicted by the QTM model against both experiment and data in literature showed a relative error less than 20%. This QTM, together with the TCN, offers a framework for rapid, part-scale simulations of Metal PBF that can be used to optimize the build process and parameters.
Recommended Citation
H. Peng and M. Ghasri-Khouzani and S. Gong and R. Attardo and P. Ostiguy and R. B. Rogge and B. A. Gatrell and J. Budzinski and C. Tomonto and J. Neidig and M. R. Shankar and R. Billo and D. B. Go and D. Hoelzle, "Fast Prediction Of Thermal Distortion In Metal Powder Bed Fusion Additive Manufacturing: Part 2, A Quasi-static Thermo-mechanical Model," Additive Manufacturing, vol. 22, pp. 869 - 882, Elsevier, Aug 2018.
The definitive version is available at https://doi.org/10.1016/j.addma.2018.05.001
Department(s)
Mechanical and Aerospace Engineering
Keywords and Phrases
Additive manufacturing; Direct metal laser sintering; Powder bed fusion; Quasi-Static; Thermal distortion; Thermal stress; Thermo-Mechanical
International Standard Serial Number (ISSN)
2214-8604
Document Type
Article - Journal
Document Version
Citation
File Type
text
Language(s)
English
Rights
© 2023 Elsevier, All rights reserved.
Publication Date
01 Aug 2018
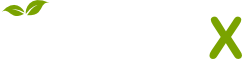
- Citations
- Citation Indexes: 46
- Patent Family Citations: 1
- Usage
- Downloads: 36
- Abstract Views: 9
- Captures
- Readers: 103
Comments
Air Force Research Laboratory, Grant FA8650-12-2-7230