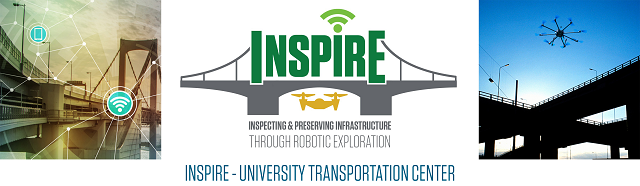
INSPIRE Archived Webinars
Webinars from 2024
Main hardware and software systems developed in the INSPIRE University Transportation Center from 2017 to 2024 will be presented. Their characteristic parameters, operation procedures, performance metrics, advantages over the state of practice, and application limitations will be summarized. These systems include, but not limited to,
Flying and climbing robots for high-quality data collection from remote sensing and nondestructive testing,
Explainable artificial intelligence and machine learning for element segmentation and defect classification,
3D reconstruction and digital twins for virtual inspection,
Framework for the probability of detection for various defects and damage from in-situ sensors,
Defect detection, location, quantification, and visualization, and
Pilot/inspector training simulator for the use of advanced technologies in automated bridge inspection.
Recent Development on Bridge Inspection Robot Deployment Systems (BIRDS), Genda Chen
Streaming video available
To meet federal requirements for new data collection, Bridge Inspection Robot Deployment Systems (BIRDS) at the INSPIRE University Transportation Center expand their capabilities for the field tests of real-world bridges. This webinar will introduce the design and testing of new robots that are interactive with bridges for high-quality inspection tasks, which is also applicable to local maintenance, and data fusion for 3D reconstruction to support bridge asset management. Specific strategies for the BIRDS advancement include: (1) A hybrid flying and traversing vehicle is attached to bridge girders as a stationary inspection platform to inspect bridge decks, girders, and piers and collect high-quality data from RGB and infrared cameras as well as a lidar scanner; (2) An unmanned aerial vehicle (UAV) carries and launches a small lightweight crawler to inspect steel members and connections in great details through a microscope or a crack probe; and (3) An UAV is equipped with an aerial manipulator for tele-maintenance, such as screwing and drilling tasks, and nondestructive testing, such as ground penetrating radar, of reinforced concrete members for defect detection and localization. More than 42% of over 617,000 U.S. bridges are 50 years (design life) or older. It is thus imperative to meet more frequent and more rigorous preservation needs to ensure that the aging infrastructure is safe during everyday operations and resilient to increasing catastrophic events associated with climate change. In recent years, inspection data are increasingly being used to support a more proactive approach of asset management to make structures not only safe but also maintainable to minimize life-cycle costs. This broadening of inspection scope requires a significant shift in practice from fully visual inspection to partially visual inspection supplemented with advanced technologies such as remote sensing, nondestructive evaluation, and structural monitoring. These technologies enable the implementation of objective decision-making processes in asset management and the understanding of infrastructure resilience.
Multi-User Collaboration in Mixed Reality for Beyond-Visual-Line-of-Sight Bridge Inspection Using Robotic Platforms, Genda Chen
Streaming video available
The U.S. National Bridge Inventory has approximately 600,000 bridges that cross rivers and roadways. These elevated structures present access challenges, resulting in inefficient and ineffective routine inspections. Visual inspection often causes traffic interruption and safety concerns, leading to inherently inconsistent condition-state assignments depending on human factors. Robotic and sensing technologies will transform the manual inspection into automated bridge inspection toward data-driven bridge management. The current application of unmanned aerial vehicles (UAVs) is limited to the visual line of sight, which is impractical for long-span bridges. In June 2023, the Federal Aviation Administration (FAA) approved several organizations to fly unmanned vehicles beyond the visual line of sight (BVLOS). Even so, UAVs are prone to crashing during short flights and require pilot licensing and stable control for high-quality data collection. For long-span bridges and the overpasses of active roadways, there is a need to seek a complimentary robotic platform for the BVLOS inspection. In this presentation, we will introduce an augmented reality framework for a multi-user collaborative system to support inspection tasks. In a case study, two inspectors collaborate at a simulated bridge site. The lead inspector ensures safety, collects visual inspection data, and retrieves historical information as needed for on-site defect investigation, while the assistant inspector navigates a magnetically wheeled structural crawler and conducts ultrasonic thickness measurements on steel bridges or components. The virtual collaboration mechanism will be integrated into a Human-centered Automated Bridge Inspection Training Simulator (HABITS) for pilots/inspectors.
Webinars from 2023
Multidimensional Digital Twin in the Built Environment to Support Multifunctional Modeling for Broader Impacts, Genda Chen
Streaming video available
Digital twin (DT) has been developed for a single function in most of previous studies. This study aims to empower DT with a multilayered integration of multifunctional and multidisciplinary models in the built environment. It starts with the development of a framework of three hierarchical tiers of regional, asset, and system DT modules, defines a new concept of the degree of digital twinning (DODT) to a real world by the number of models enabled by a common DT platform, enables spatiotemporal analysis in multiple scales to couple nonstructural with structural building components and connect the built environment to planning constructions, enables an integrated computational and informational modeling, and demonstrates multiple values of the DT of a university campus in asset lifecycle management. A mechanical model is used to evaluate the structural and nonstructural behavior of buildings under earthquake loads, allowing damage/cost scenario studies for community resilience in the wake of an extreme event. A multitask machine learning model is used to detect the type and material of building roofs from videos, allowing infrastructure planning for existing buildings. An informational model allows master planning for green space development, environmental planning for flood zone susceptibility, security protocol development, and energy harvesting and utilization. The DODT allows the value-driven digital replication of a physical twin at different levels and thus the value proposition of structural health monitoring in broader architectural and engineering practices. The DODT of the campus is eight, indicating that the DT has broader impacts on campus' asset lifecycle management.
Robotic Inspection of Infrastructure Using Vision, GPR, and Impact-Echo Sensors, Jizhong Xiao
Streaming video available
Bridges, dams, highways, and tunnels in the U.S. are reaching their life expectancy, and thus have imperative needs for routine inspection and maintenance to ensure sustainability. It is reported that 42% of over 600,000 highway bridges in the National Bridge Inventory (NBI) have exceeded their design life of 50 years, and 42,951 bridges are rated in poor condition and classified as "structurally deficient". To inspect the structurally integrity of bridges, the inspectors also need to detect subsurface defects (i.e., delamination, voids) using NDE instruments such as GPR and impact-echo (IE) device at difficult to access components (i.e., pier, bottom side of the deck). The current practice of manual inspection hand-held NDE devices by a "spider-man" with rope access, or by using scaffolding or by using snooper truck has to block traffic, and is expensive, time-consuming, and exposes human inspectors to dangerous situations. This presentation will introduce climbing robots developed over the years at CCNY Robotics Lab that integrate the robot control and vision-based accurate positioning with NDE signal processing to detect both surface flaws and subsurface defects. The use of the robotic inspection tool will eliminate the time, hassle, and cost to layout grid lines on flat terrain, and make it possible to automatically collect NDE data with minimum human intervention. This presentation will also introduce machine learning algorithms for visual inspection to detect and measure cracks: IE data processing methods that utilizes both learning-based and classical methods to interpret the IE data and reveal subsurface objects; and DNN-based GPR data analysis software to reveal subsurface targets for better visualization.
Probability of Detection in Structural Health Monitoring, Genda Chen
The fundamental concept of the probability of detection in structural health monitoring is introduced. The traditional Probability of Detection (POD) method as described in the Department of Defense Handbook MIL-HDBK-1823A for nondestructive evaluation systems does not take the time dependency of data collection into account. When applied to in-situ sensors for the measurement of flaw sizes, such as fatigue-induced crack length and corrosion-induced mass loss, the validity and reliability of the traditional method is unknown. In this 50-minute lecture, the POD for in-situ sensors and their associated reliability assessment for detectable flaw sizes are evaluated using a Flaw-Size-at-Detection (FSaD) method and a Random Effects Generalization (REG) model. Although applicable to other sensors, this presentation is focused on long period fiber gratings (LPFG) corrosion sensors with thin Fe-C coatings. The FSaD method uses corrosion-induced mass losses when successfully detected from different sensors for the first time, while the REG model considers the randomness and difference between mass loss datasets from different sensors. The Fe-C coated LPFG sensors were tested in 3.5 wt.% NaCl solution until the resonant wavelength of transmission spectra no longer changed or the Fe-C coating was oxidized completely. The wavelength shift of 70% of the tested sensors ranged from 6 to 10 nm. In comparison with the FSaD method, the REG method is more robust to any departure from model assumptions since significantly more data are used in the REG method.
Webinars from 2022
Structural Inspection Automation: Research Challenges and 3D Machine Vision Techniques, ZhiQiang Chen
Streaming video available
This presentation will start by reviewing the history of vision or imaging-based structural (surface condition or damage) inspection and discuss the notion of structural inspection automation. Besides robotic platforms for operation, this conceived automation process must feature 3-dimensional (3D) integrated structural element and damage (or any anomaly) detection, quantification, and mapping amid complex scenes. Further, the results of such a process should be readily fused with existing lifecycle 3D BIM or digital-twin models (DTMs) for ultimate decision-making.
The presentation plans to discuss that machine vision with optical sensors is the most viable approach as a core component to realizing structural inspection automation. Using an analogy of Tesla cars that rely entirely on vision sensors without using active Radar or LiDAR sensors, the presentation will then elaborate on six automation levels for structural inspection. However, our civil infrastructure stakeholders are much different from those from private automobile sectors, which have poured tremendous investment into collecting and creating semantically rich datasets for developing machine learning algorithms and AI-based software frameworks. On the other hand, large-scale semantically annotated datasets from civil engineering sectors are not expected to be available in the near future. Considering such constraints and aiming at the goal of realizing cost-effective structural inspection automation, the presentation will introduce recent efforts in the following three topics:
- Low-cost 3D structural element and damage data collection and deep learning based algorithmic benchmarking
- Human-in-the-loop based structural data collection using augmented reality headsets.
- Visual Simultaneous localization and mapping (SLAM) enabled optimal structural element and damage mapping using virtual reality-based robotic drones.
The presentation will conclude by sharing the vision and opportunities about the future of this research area.
Reliability of Bridge Inspection Technologies, Glenn A. Washer
Streaming video available
This presentation will discuss the reliability of inspection technologies used for the condition assessment of highway bridges. Data from condition assessments are critical to asset management and decision-making. The methodologies used to assess condition are usually subjective methods, such as visual inspections, that can vary as a result of human factors and differences in training and interpretation of inspection procedures. Nondestructive evaluation technologies (NDE) are implemented on a more limited basis and rely on indirect measurements to infer the presence of damage, and these assessments are affected by environmental factors, materials variability, and limitations in the interpretation of the resulting data. Field studies of inspection quality for element-level (CSs) and component-level (CRs) results will be discussed that illustrate the variability in data from routine inspections of highway bridges. Methods implemented in recent years to improve the quality of these inspections will be discussed. Variability in several common NDE techniques will also be discussed, such as Ground Penetrating Radar (GPR), Infrared Thermography (IRT), and Ultrasonic Testing (UT), based on results from field studies and performance tests. The impact of the reliability of these technologies of the future of bridge inspection, including risk-based inspection decision-making, will be addressed as a conclusion to the presentation.
Intelligent Human-Infrastructure Interfaces for Inspectors and Decision-Makers, Fernando Moreu
Streaming video available
This seminar challenges the traditional conversation about digital twins and machine learning, by proposing a different paradigm for smart cities transformation centered in new human-infrastructure interfaces. This discussion explores the area of human decisions and cognition of the built environment enabling transformations of human interacting with structures in a new environment. To date, new technologies collecting data of the built environment are cheaper, more accurate, diverse, and more accessible than ever before. However, the use and implementation of these new technologies to structural engineers to assess, inspect, or inform actions have been very limited. Decision-makers, owners of infrastructure, policy makers, occupants, and inspectors of infrastructure are often not considered when developing new technologies to inform structural responses or condition. By empowering human-machine interfaces and fostering human involvement and participation (human-in-the-loop), this seminar will present specific practical implementations about how the collection of data, their analysis, and their interpretation can inform (and transform) human decisions. Specific applications include the connection of Augmented Reality with Wireless Sensors Networks, AI, ML, Structural Dynamics, and Inspections.
Toward Dexterous Aerial Manipulation using Embodied Human-Intelligence for Bridge Inspection and Maintenance, Dongbin Kim
Streaming video available
Current drones perform a wide variety of tasks in surveillance, photography, agriculture, package delivery, etc. However, these tasks are performed passively without the use of human interaction. Aerial manipulation shifts this paradigm and implements drones with robotic arms that allow interaction with the environment rather than simply sensing it. Many research groups have demonstrated aerial manipulation for various applications for over a decade. For example, in construction, aerial manipulation in conjunction with human interaction could allow operators to perform several tasks, such as hosing decks, drill into surfaces, and sealing cracks via a drone. This integration with drones will henceforth be known as dexterous aerial manipulation. However, there are still no implementation and adoption in practical applications.
To overcome this issue, we recently integrated the worker’s experience into aerial manipulation using haptic technology. The net effect was such a system could enable the worker to leverage drones and complete tasks while utilizing haptics on the task site remotely. However, the tasks were completed within the operator’s line-of-sight. Until now, immersive AR/VR frameworks has rarely been integrated in aerial manipulation. Yet, such a framework allows the drones to embody and transport the operator’s senses, actions, and presence to a remote location in real-time. Thus, AR/VR technology enables the operator to leverage their intelligence to collaboratively perform desired tasks anytime, anywhere with a drone that possesses great dexterity. Finally, the operator can both physically interact with the environment and socially interact with actual workers on the worksite. Toward this vision, this work presents aerial manipulation using embodied human intelligence.
Webinars from 2021
Hyperspectral Imaging and Data Analytics for Civil Infrastructure Inspection, Genda Chen
Streaming video available
In this 50-minute lecture, the fundamental concept of hyperspectral imaging is reviewed. Each hyperspectral image represents a narrow, contiguous wavelength range of an electromagnetic spectrum, which could be indicative of a chemical substance. All the images in the spectral range of a hyperspectral camera are combined to form a three-dimensional hyperspectral data cube with two spatial dimensions and one spectral dimension. A hyperspectral cube can be sampled in four ways: spatial scanning, spectral scanning, snapshot imaging, and spatio-spectral scanning. This presentation will be focused on spatial scanning from a line-scan camera. The feasibility of horizontal imaging from a synchronized hyperspectral camera and LiDAR scanner system will be explored first. The hyperspectral images are then applied into several infrastructural inspections: concrete roadway condition assessment, fresh mortar strength evaluation, chloride concentration determination in reinforced concrete, steel reinforcing bar and steel plate corrosion, and surface plant stress monitoring as an indication of gas leakage from embedded pipelines. As an example, mortar samples with a water-to-cement (w/c) ratio of 0.4-0.7 were cast and scanned during curing. Reflectance data at a wavelength range of 1920 nm to 1980 nm, associated with the O-H chemical bond, were averaged to classify different mortar types with a Support Vector Machine (SVM) algorithm and predict their compressive strength from a regression equation. After baseline and bias corrections, the reflectance intensity at 2258 nm wavelength was extracted to characterize Friedel’s salt. The possibility of steel corrosion was experimentally shown to increase with the characteristic reflectance intensity that in turn decreases linearly with the diffusion depth at a given corrosion state. For each type of mortar cubes with a constant w/c ratio, the characteristic reflectance intensity linearly increases with chloride ion Cl- concentration up to 0.8 wt.%.
Image-Based Bridge Defect Detection and Monitoring Technologies, Jian Zhang
Streaming video available
Computer-vision is an emerging technology which has been widely used in the field of structural health monitoring. This seminar will cover the latest achievements of our research group in defect detection, health monitoring, and construction control using image-based technologies. For defect detection, advanced unmanned aerial vehicles (UAVs) have been developed to automatically detect surface cracks and other types of structural damages based on digital image processing techniques. An integrated navigation system combining binocular camera and inertial sensor enables automated route planning for the developed UAVs in case of GPS failure. Specifically, a wall-climbing UAV is designed to acquire detailed surface crack images with high accuracy and a collision-tolerant UAV is proposed for the defect inspection of complex or internal spaces. In addition to UAV, an unmanned ship is developed for exploration of inaccessible places such as sewers. For structural health monitoring, on-line camera monitoring system has been developed for displacement measurement of long-span bridges. For construction control, a binocular vision-based method is investigated and applied for displacement measurement during the hoisting process of prefabricated components. Experimental results show that compared to conventional methods, the proposed approach is more intelligent, more convenient, and more reliable.
Fiber Optic Sensor Based Corrosion Assessment in Reinforced Concrete Members, Genda Chen
Streaming video available
In this 50-minute lecture, the fundamental concepts of fiber optic sensors for both distributed and point corrosion measurements are reviewed. For the distributed monitoring of a line bridge component such as steel reinforced girders, Brillouin scattering and fiber Bragg gratings (FBG) can be coupled to measure both temperature and radial strain as an indirect indicator of corrosion process. For the point monitoring of steel structures, long period fiber gratings (LPFG) are specially designed for a direct measurement of mass loss or the loss in cross sectional area of the component. In particular, a Fe-C coated LPFG sensor is introduced for corrosion induced mass loss measurement when Fe-C materials are comparative to the parent steel component to be monitored. The sensing system operates on the principle of LPFG that is responsive to not only thermal and mechanical deformation, but also the change in refractive index of any medium surrounding the optical fiber. Fabrication process of the LPFG is demonstrated through the CO2 laser aided fiber grating system. To enable mass loss measurement, a low pressure chemical vapor deposition (LPCVD) system is introduced to synthesize a graphene/silver nanowire composite film as flexible transparent electrode for the electroplating of a thin Fe-C layer on the curve surface of a LPFG sensor. An integrated sensing package is illustrated for corrosion monitoring and simultaneous strain and temperature measurement. Two bare LPFGs, three Fe-C coated LPFG sensors are multiplexed and deployed inside three miniature, coaxial steel tubes to measure critical mass losses through the penetration of tube walls and their corresponding corrosion rates in the life cycle of an instrumented steel component. The integrated package can be utilized for in-situ deterioration detection in reinforced concrete and steel structures. Assisted by a permanent magnet in pipeline monitoring, both FBG and LPFG sensors are combined with an extrinsic Fabry-Perot interferometer (EFPI) to measure both internal and external thickness reductions without impacting the operation of the pipeline.
Human-Robot Collaboration for Effective Bridge Inspection in the Artificial Intelligence Era, Ruwen Qin
Streaming video available
Advancements in sensor, Artificial Intelligence (AI), and robotic technologies have formed a foundation to enable a transformation from traditional engineering systems to complex adaptive systems. This paradigm shift will bring exciting changes to civil infrastructure systems and their builders, operators and managers. Funded by the INSPIRE University Transportation Center (UTC), Dr. Qin’s group investigated the holism of an AI-robot-inspector system for bridge inspection. Dr. Qin will discuss the need for close collaboration among the constituent components of the AI-robot-inspector system. In the workplace of bridge inspection using drones, the mobile robotic inspection platform rapidly collected big inspection video data that need to be processed prior to element-level inspections. She will illustrate how human intelligence and artificial intelligence can collaborate in creating an AI model both efficiently and effectively. Obtaining a large amount of expert-annotated data for model training is less desirable, if not unrealistic, in bridge inspection. This INSPIRE project addressed this annotation challenge by developing a semi-supervised self-learning (S3T) algorithm that utilizes a small amount of time and guidance from inspectors to help the model achieve an excellent performance. The project evaluated the improvement in job efficacy produced by the developed AI model. This presentation will conclude by introducing some of the on-going work to achieve the desired adaptability of AI models to new or revised tasks in bridge inspection as the National Bridge Inventory includes over 600,000 bridges of various types in material, shape, and age.
Webinars from 2020
Artificial Intelligence-Empowered Civil Engineer, Hui Li
Streaming video available
Artificial intelligence (AI) is an emerging cutting-edge technology, which have generated great impact to social science, business, medicine, natural science and engineering. The applications of AI will bring revolution to civil engineering in all sides. Most attractive concerns in natural science and engineering are that if we can create “AI-empowered SCIENTIST” and “AI-empowered CIVIL ENGINEER”. This seminar will focus on the “AI-empowered CIVIL ENGINEER” who can do design, fabrication, analysis, maintenance and disaster risk management by machine learning (ML) and deep learning. Specifically, the design of materials and the prediction of properties of materials by ML is first presented. The ML-based architecture design and topological design of structures are then introduced. Finally, a systematic approach for the ML-assisted health monitoring of structures is proposed to cover the topics such as abnormal data diagnosis, loss data recovery, modal identification, damage detection and condition assessment, load identification, and 3D model reconstruction. The applications of ML in wind engineering is also introduced.
UAV-enabled Measurement for Spatial Magnetic Field of Smart Rocks in Bridge Scour Monitoring, Genda Chen
Streaming video available
This lecture will present an overview of the research, development, validation, and implementation of 'smart' rocks as in-situ agents to assist in remote monitoring of bridge scour in real time. It will start with a brief review of fundamental concepts such as magnet, polarization, magnetic field, and field measurement principle. It will then introduce the concept of ‘smart’ rocks, demonstrate it through small-scale laboratory tests, and design and fabricate gravity-controlled ‘smart’ rocks for field implementation based on river hydrodynamics and riverbed conditions. Next, a ‘smart’ rock localization optimization algorithm will be formulated analytically and validated experimentally in open fields. It will be followed by the integration of magnetic field measurements into a mobile unmanned aerial vehicle (UAV) including a global positioning system. Finally, this lecture will present the field test and simulation results at a bridge site and data interpretation to determine a critical engineering parameter - maximum scour depth in the past three years. Overall, a properly-designed ‘smart’ rock consistently moved down the bottom of a scour hole through repeated laboratory tests. Each UAV-supported field test lasted for about 10 minutes. The ‘smart’ rock positioning at the bridge site is consistent with an accuracy of approximately 0.3 m. ‘Smart’ rocks is a promising technology to mitigating the effects of bridge scour, which is the main reason for the collapsing of over 1,500 bridges in the U.S.
Mobile Manipulating Drones, Paul Oh
Streaming video available
In the past few years, robotic limbs have been attached to rotorcraft drones to perform aerial manipulation. Unlike simple object pick-and-place, such mobile-manipulating drones are dexterous to perform tasks like valve-turning, hatch-opening, and tool-handling. This is a paradigm shift where such drones actively interact with their environment rather than just passively surveil. Aerial manipulation is challenging because such interaction yields reaction forces and torques that destabilize the drone. This talk will provide an overview of aerial manipulation and showcase examples that could serve in infrastructure inspection, maintenance, and repair.
Non-Contact Air-Coupled Sensing for Rapid Evaluation of Bridge Decks, Jinying Zhu
Streaming video available
Elastic wave-based non-destructive testing (NDT) methods are commonly used for evaluation of civil engineering infrastructure, including bridges, dams and buildings. However, most of these methods require coupling (direct contact) between sensors and the test surface, which significantly restricts the testing speed and consistency, especially for large scale concrete structures in civil engineering. The air-coupled sensing technology was developed by Dr. Jinying Zhu as a solution for rapid scanning of concrete infrastructure. In this webinar, Dr. Zhu will review the development of air-coupled sensing technique for civil engineering applications, including fundamental theory and field application of air-coupled sensing on concrete structures. She will also present a recently developed automated acoustic scanning system for quick bridge deck evaluation and imaging.
Webinars from 2019
Simulation Training and Route Optimization for Bridge Inspection, Sushil Louis
Streaming video available
Since the 1970s, simulation training has developed operational trainers for a variety of complex systems from pilot flight simulations to cultural awareness training simulations. When connected to the real world, such simulation training interfaces can drive real vehicles and systems. We have been building a Simulation Training And Control System (STACS) for autonomous bridge inspection that uses a simulated world to train inspectors to control a heterogeneous group of robots. The objective is that, once trained, inspectors can use the same STACS interface used in training to control multiple real robots simultaneously during a bridge inspection task. We first built a multi-robot control interface and simulated environment so that a single operator may manage at least two types of robots. Second, we developed a new optimization algorithm for automatically and quickly generating near-optimal routing for n robots to cooperatively cover every truss while minimizing inspection time. This webinar describes and demonstrates STACS, provides optimization results corresponding to time (and thus cost) saved in bridge inspection. Results show that we can significantly reduce bridge inspection time with inspection robots and that the time needed decreases in inverse proportion to the number of robots available for inspection.
Data to Risk-Informed Decisions through Bridge Model Updating, Iris Tien
Streaming video available
Across the country, bridge structures are aging with use commonly extending beyond their original design lives. Decisions to repair, retrofit or rehabilitate these structures will support continued reliability and resilience of these structures. To better understand the states of the bridges at any point in time, there are new technologies to inspect, monitor and assess bridge conditions.
To effectively use the results of these inspections and monitoring activities, we need an understanding of the relation between varying inspection parameters and the predicted performance of bridge structures.
In this seminar, we will describe methods to use inspection data to update assessment of bridge performance, focusing on corrosion inspection data. Through bridge model updating, we account for the effects of corrosion, including reduction of longitudinal and transverse reinforcement and bond deterioration between the steel and concrete through corrosion-induced cracking in reinforced concrete bridges. Corrosion is measured by percent mass loss. The impact of measured corrosion parameters on performance is assessed with results quantifying the increase in risk or vulnerability of these structures as corrosion levels increase. Comparing results across bridges supports risk-informed decisions in the management of bridges to protect these structures and ensure their reliability and resilience under future loading and hazard scenarios.
Performance Based Design for Bridge Piers Impacted by Heavy Trucks, Anil K. Agrawal
Streaming video available
Based on bridge failure data compiled by New York State Department of Transportation, collision, both caused by vessel and vehicles, is the second leading cause of bridge failures after hydraulic. Current AASHTO-LRFD (2012) recommends designing a bridge pier vulnerable to vehicular impacts for an equivalent static force of 600 kips (2,670 kN) applied in a horizontal plane at a distance of 5.0 feet above the ground level. This research presents a performance-based approach for designing a bridge pier subject to impacts by tractor-semi-trailer weighing up to 80,000 lb based on an extensive investigation using finite element model of a tractor-semitrailer in LS-DYNA. In order to ensure the reliability of the proposed approach, parameters of concrete model were calibrated using small-scale impact test and were validated using a large scale test. Mechanics and modes of failure of bridge pier bents during vehicular impacts were verified through pendulum impact test on a large scale model of three column pier-bent system. A performance-based approach in terms of shear distortion, plastic rotation and demand / capacity (D/C) ratio has been proposed for the design of bridge piers vulnerable to heavy vehicle impacts.
Battery-Free Wireless Strain Measurement using an Antenna Sensor, Yang Wang
Streaming video available
A battery-free antenna sensor can wirelessly measure strain on a structure. Bonded to the surface of a base structure, the antenna sensor deforms when the structure is under strain, causing the antenna’s electromagnetic resonance frequency to change. This resonance frequency change can be wirelessly interrogated and recorded by a reader through electromagnetic backscattering. A radio frequency identification (RFID) chip on the sensor harnesses a small amount of energy from the interrogation signal and responds to the reader. The resonance frequency change identified by the reader is then used to determine the strain applied on the structure. The latest antenna sensor prototype adopts a thermally stable substrate as demonstrated in outdoor tests. Considering nonlinear constitutive relations, multi-physics simulation is performed to more accurately model the behaviors of the antenna sensor. In both simulation and laboratory experiments, the antenna sensor is shown to be capable of wirelessly measuring small strain changes. Finally, an emulated crack testing of the antenna sensor is presented, demonstrating the capability of measuring crack growth in application settings.
Assistive Intelligence (AI): Intelligent Data Analytics Algorithms to Assist Human Experts, Zhaozheng Yin
Streaming video available
Artificial Intelligence, particularly deep learning, has recently received increasing attention in many applications, such as image classification, speech recognition, and computer games. The success of deep learning algorithms requires big annotated datasets for training, gradient-based optimization algorithms, and powerful computational resources. In the case of civil infrastructure inspection, we can collect big data from different imaging sensors such as color, thermal, and hyperspectral cameras. Three issues encounter in this application. First, it is tedious and expensive to let human experts annotate the datasets to train deep learning algorithms. Second, the offline trained deep learning algorithms may not be able to adapt to new civil infrastructures. Third and lastly, the trained deep learning algorithm works like a black box on new data, without the domain knowledge from human experts. In this project, we investigate intelligent data analytics algorithms with human experts in the loop, called Assistive Intelligence (AI). Using the bridge inspection as a case study, we aim to find regions-of-interest (e.g., joints with damages) over long video sequences. The data analytics algorithm is initially trained from a small set of data. Given the dataset of a new bridge, bridge experts only need to annotate a few region-of-interest examples as the seed; our algorithm will retrieve corresponding examples in the rest of videos. Human experts can also return some incorrectly retrieved samples to the data analytics algorithm for further refinement. Thus, while the data analytics algorithm can assist human in an efficient way, bridge experts can leverage their domain knowledge in the adaptation of the computational tool in different scenarios.
Webinars from 2018
Toward Autonomous Wall-Climbing Robots for Inspection of Concrete Bridges and Tunnels, Jizhong Xiao
Streaming video available
In addition to visual inspection for surface flaws, inspectors are often required to detect subsurface defects (e.g., delamination and voids) using nondestructive evaluation (NDE) instruments, such as ground penetration radar (GPR) and impact sounding device, in order to determine the structural integrity of bridges and tunnels. In these cases, access to critical locations for reliable and safe inspections is a challenge.
Since 2002, Dr. Jizhong Xiao’s group has developed four generations of wall-climbing robots for NDE inspection of bridges and tunnels. These robots combine the advantages of aerodynamic attraction and suction to achieve a desirable balance of strong adhesion and high mobility. For example, Rise-Rover with two drive modules can carry up to 450 N payload, and GPR-Rover can carry a small GPR antenna for subsurface flaw detection and utility survey on concrete structures. These robots can reach difficult-to-access areas (e.g., the bottom side of bridge decks), take close-up pictures, record and transmit NDE data to a host computer for further analysis. They can potentially make bridge inspection faster, safer, and cheaper without affecting traffic flow on roadways.
This presentation will review the recent development of smart and autonomous wall-climbing robots to realize automated inspection of civil infrastructure with minimal human intervention.
Climbing Robots for Steel Bridge Inspection and Evaluation, Hung La
Streaming video available
Steel structures and steel bridges, constituting a major part in civil infrastructure, require adequate maintenance and health monitoring. In the U.S., more than 50,000 steel bridges are either deficient or functionally obsolete, which likely presents a growing threat to people's safety. The collapse of numerous bridges recorded over the past 16 years has shown significant impact on the safety of all travelers.
In this presentation, the design and implementation of two different climbing robots for steel structure inspection are reported. Based on the magnetic wheel design, the robot can climb on different steel surface structures (i.e., flat, cylinder, cube). The robots can be remotely controlled or programmed to move autonomously on steel structures. Current tests shows that the robots can carry up to 8 pounds of load while being able to adhere strongly on the steel surface. Climbing capability tests are done on bridges and on several steel structures with coated or unclean surfaces. Although the steel surface is curved and rusty, the robots can still adhere tightly.
Microwave Materials Characterization and Imaging for Structural Health Monitoring, Reza Zoughi
Streaming video available
The relatively small wavelengths and large bandwidths associated with microwave signals make them great candidates for inspection of construction materials and structures, and for materials characterization and imaging. Signals at these frequencies readily penetrate inside of dielectric materials and composites and interact with their materials characteristics and inner structures. Water molecule is dipolar and possesses a relatively large complex dielectric constant, which is also highly sensitive to the presence of ions that increase its electrical conductivity. Consequently, chemical and physical changes in construction materials affect their complex dielectric constant. This can be measured, and through analytical and empirical dielectric mixing formulae, correlated to those changes. Examples of applications would be, presence of delamination in a bridge deck and pavement, permeation of moisture behind retaining walls or corrosion of reinforcing steel bars which can be imaged with microwave techniques. One of the critical trade-off issues is between the microwave signal penetration into concrete vs. frequency of operation. Dielectric of concrete, particularly when moist, has a relatively high loss factor. As such, lower microwave frequencies are suitable to achieve reasonable penetration. Image resolution degrades as a function of decrease in operating frequency, therefore, a balance must be reached when using these techniques for imaging cement-based materials. In this webinar, issues related to concrete materials property evaluation and high-resolution imaging will be discussed, and examples will be provided.
Webinars from 2017
Drone-Enabled Remote Sensing for Transportation Infrastructure Assessment, Colin Brooks
Streaming video available
Unmanned aerial systems (UAS or “drones”) are a rapidly developing technology that can help meet the needs of transportation agencies for reliable, repeatable data that can save money and increase safety for the data collection process. By taking advantage of flexible platforms that can deploy a variety of sensors, transportation agencies and their information suppliers can help meet these data needs for operations, asset management, and other areas. Location-specific data on infrastructure condition and distresses can help with improved management of assets.
In this presentation, recent applied research led by a Michigan Technological University team is reviewed, with a focus on bridge condition assessment and corridor monitoring. Examples of 3D optical, thermal, and LiDAR data are shown and how analysis methods result in usable information to meet pressing data needs. Finding spalls and delaminations, characterizing cracking, inventory of roadway assets, and related applications will be shown. Achievable resolutions and accuracies will be reviewed and how these data are transformed into asset condition data.
Lab-on-Sensor for Structural Behavior Monitoring: Theory and Applications, Genda Chen
Streaming video available
There are over 600,000 bridges in the U.S. National Bridge Inventory (NBI). Nearly 50% of them rapidly approach their design life and deteriorate at an alarming rate, particularly under an increasing volume of overweight trucks. Visual inspection as the current practice in bridge management is labor intensive and subjective, resulting in inconsistent and less reliable element ratings. Lab-on-sensor technologies can provide supplemental mission-critical data to the visual inspection for both qualitative and quantitative evaluations of structural conditions, and thus critical decision-making of cost-effective strategies in bridge preservation.
In this presentation, the design and operation characteristics of highway bridges are first reviewed to establish the needs for structural behavior monitoring in order to align monitoring outcomes with daily practices in bridge preservation. Next, a lab-on-sensor design theory is presented and applied to detect and assess structural behaviors such as concrete cracking, foundation scour, and steel corrosion. Finally, the accuracy, resolution and measurement range of various sensors are discussed before this presentation is concluded.