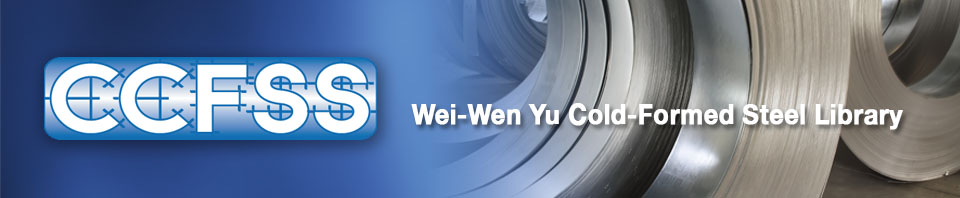
CCFSS Library (1939 - present)
Abstract
SUMMARY In conjunction with research projects on diaphragm-braced members conducted at Cornell University, this investigation deals with the function of the fasteners in the braced system. In these systems, the diaphragm resists the lateral deflections of the braced members, in its plane, by virtue of its shear regidity (Qdr) and its shear strain capacity Yd (as a measure of strength). Considering the system in a slightly deformed shape, compatibility of displacements and forces between the diaphragm and the braced member at their connection locations, implies that the fasteners at these locations are subjected to the action of a system of internal forces defined as the fastener forces. The analysis herein is concerned with the location of the critical fastener and the forces acting on it, rather than the distribution of these forces in all the fasteners along the member. The shear characteristics of the diaphragm (Qdr,Yd ) are obtained either by conducting a cantilever test for each case under consideration, or when available, from catalogues which are favored for practical design purposes even though it is unlikely that a catalogue will contain diaphragms of dimensions identical to the structure. Fastener strength may be determined experimentally by the use of the device suggested in appendix 2, or from fastener strength catalogues. The design of diaphragm-braced members according to the procedure presented in Report No. 332 "Design Recommendations for Diaphragm-Braced Beams, Columns, and Wall Studs" requires, as a check to the diaphragm adequacy, that the diaphragm shear rigidity (Qdr) and its shear strain capacity (Yd ) determined from a cantilever test, should be greater than the calculated value of the shear rigidity required for full bracing (Qid) and the maximum shear strain (Ymax ) in the structure respectively. Those requirements were found to be necessary in all cases, however in some, they are insufficient and an additional requirement has to be satisfied, namely, the maximum fastener force in the actual structure (Fmax ) has to be less than the fastener strength (Ff ). See Appendix 1. The magnitude of (Fmax ) was found to be a function of the diaphragm shear rigidity (Qdr) and the maximum shear strain in the diaphragm (Ymax ). The later parameter is determined by utilizing the formulas of Report No. 332. Part 4 of this report presents numerically two design examples for calculating (Fmax ), with illustration on the use of the cantilever test and of diaphragm catalogues to determine (Qdr) for the analysis. An attempt to determine an approximate, but rather conservative value of the maximum fastener force in the diaphragm cantilever test, is included in Appendix 3. The analysis of a tested cantilever gives a predicted failure load 7.5% lower than that reached in the test. The location of the critical fastener and the magnitude of the maximum fastener force was found to be influenced by the diaphragm boundary conditions as well as the end conditions of the braced member. For example in diaphragms, fastened along four sides, the fastener force is not critical, on the other hand if the diaphragm is fastened only along two sides, the fastener force governs the design, accordingly in the former case the checking procedure of Report No. 332 regarding (Qdr,Yd ) is sufficient to insure the diaphragm adequacy, while in the latter, the additional requirement of the fastener strength has to be satisfied. In a system of flexurally hinged end members the critical fastener is the one close to the ends of the member. For a fixed end conditions, it is the one close to the point of inflection of the deflected member. It is suggested herein that the fastener forces in addition to (Qdr,Yd) requirements, be checked for all cases in which the diaphragm shear characteristics are determined from diaphragm catalogues. However, if the cantilever test is used, the fastener force has to be checked only in the case described above. Otherwise the procedure of Report No. 332 is fully adequate for the design.
Department(s)
Civil, Architectural and Environmental Engineering
Sponsor(s)
American Iron and Steel Institute
Research Center/Lab(s)
Wei-Wen Yu Center for Cold-Formed Steel Structures
Publication Date
01 May 1971
Document Version
Final Version
Document Type
Technical Report
File Type
text
Language(s)
English
Technical Report Number
Report No. 341
Recommended Citation
Simaan, Amir; Winter, George; and Peköz, Teoman, "Fastener strength in diaphragm braced members" (1971). CCFSS Library (1939 - present). 20.
https://scholarsmine.mst.edu/ccfss-library/20