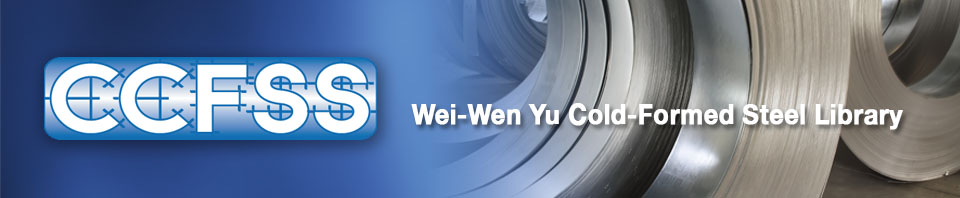
CCFSS Library (1939 - present)
Abstract
Light gage steel roof, wall, and floor systems may be used to transfer in-plane shear forces from one part of a framed structure to another, leading to reduced loads in parts of the structure. This is particularly noticeable in buildings having rigid end walls and under lateral loading. The diaphragms transfer forces from the interior frames into the foundation through the rigid end walls, resulting in lower loads for the interior frames. The amount of force transfer is dependent upon the in-plane shear strength and is particularly sensitive to the shear stiffness of the diaphragm. The results from some 60 full scale diaphragm shear tests and several smaller tests are presented. The test diaphragms were fabricated from several different panel shapes and thicknesses and had three basic types of connections. These were welds, screw type fasteners, and backed up fasteners. The assembly method generally followed that recommended by the panel manufacturer except in a few cases where it was desirable to study the influence of fastener spacing. The tests included 22, 26, and 28 gage diaphragms under static, pUlsating, and reversed loading. It is shown that the shear strength per foot of diaphragm is relatively independent of length along the corrugations provided a regular fastener arrangement is used throughout. The addition of sidelap fasteners increases the shear strength in proportion to the number of fasteners added. The strength is also dependent on the intensity and number of cyclic loads, being lower than the static strength if the number of cycles is large and the cyclic load is intensive. However, cyclic loads up to ~ 0.3 of the static strength and applied for up to 30 cycles, result in only a small strength reduction. A critical measure of diaphragm performance is the shear stiffness. For a given panel configuration and a fixed fastener arrangement, the stiffness is very strongly dependent on the panel length. This is due to the introduction of accordionlike warping across the panel ends which penetrates into the diaphragm and reduces the shear stiffness. The penetration is relatively independent of length and as the diaphragm becomes longer, the warping influence at the ends becomes less significant. This accounts for a variation in shear stiffness with length. A method is presented to predict the shear stiffness for diaphragms of any length on the basis of a single test. A method of analysis for framed structures having diaphragms is given and it is illustrated by simple examples. Gable frame mill buildings are investigated in considerable detail by theoretical means as well as by model analysis. The investigation shows that roof diaphragms are very influential in reducing interior frame loads when the buildings have stiff end walls. Load factors for light gage steel diaphragms under inplane shear were determined on the basis of extensive reversed load tests. The factors were derived within the framework of the American Iron and Steel Institute Light Gage ColdFormed Steel Design Manual (1962) Specifications. The recommended values cover wind loads, earthquake loads, dead loads, and gravity live loads.
Department(s)
Civil, Architectural and Environmental Engineering
Sponsor(s)
American Iron and Steel Institute
Research Center/Lab(s)
Wei-Wen Yu Center for Cold-Formed Steel Structures
Publisher
Cornell University
Publication Date
01 Aug 1965
Document Version
Final Version
Rights
© 1965 Cornell University, All rights reserved.
Document Type
Technical Report
File Type
text
Language(s)
English
Technical Report Number
Report No. 319
Recommended Citation
Luttrell, Larry D. and Winter, George, "Structural performance of light gage steel diaphragms" (1965). CCFSS Library (1939 - present). 140.
https://scholarsmine.mst.edu/ccfss-library/140