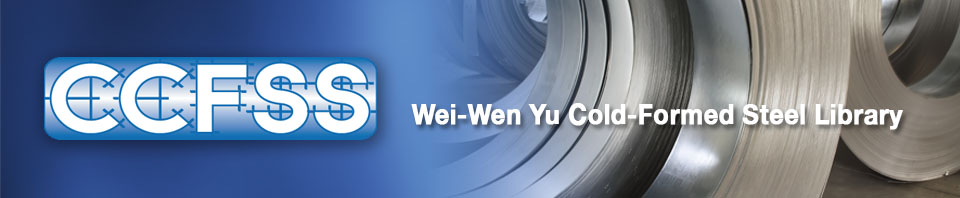
CCFSS Library (1939 - present)
Alternative Title
Civil Engineering Study 96-4
Abstract
This second progress report describes the design of deck panel specimens for flexural tests and presents the test results of ninety-three deck panel specimens. The deck panels consisted of single and multiple hat-shaped ribs in their cross sections and were manufactured from 28, 26, and 22 gage steel sheets of Structural Grade 80 of ASTM A653 Steel. Among the ninety-three deck panel specimens, seventy-two panels were tested in simply supported and two-point loading conditions; sixteen panels were tested in simply supported and one-point loading conditions; and five panels with screws penetrating through tension flanges were tested in simply supported and two-point loading conditions. Three yielding conditions were considered in the design of the deck panel specimens, namely first yielding occurring in compression flange only, first yielding occurring in both compression and tension flanges simultaneously, and first yielding occurring in tension flange only. The specimens and the test setup were designed to ensure only a flexural failure mode. The actual average w/t ratio of the specimens ranged from 17.93 to 189.95 and the actual average h/t ratio ranged from 17.67 to 104.43. The actual average angle between planes of the web and bearing surface varied from 59.06 to 62.21 degree. The actual average yield strength of the sheet steels varied from 103.9 to 112.5 ksi. For the two-point loading condition, the test results indicated that for the panel specimens with small w/t ratios (17.93 to 61.07), the tested yield moments were reached and compared reasonably well with the calculated effective yield moments using actual dimensions, actual yield strength of the steel, and the 1986 AISI Specification. However, for the panel specimens with large w/t ratios (102.86 to 189.95), the tested ultimate moments were lower than the calculated effective yield moments using actual yield strength of the steel, but much larger than the calculated moments using the 75% of the specified minimum yield strength of the steel (that is 60 ksi), and even larger than the calculated moments using 100% of the specified minimum yield strength of the steel (80 ksi). Panel specimens designed for the first yielding in the tension flange developed higher ratios of tested yield moment to calculated effective yield moment. Higher tested yield moment to weight-per-Iength ratio of the panel was achieved for specimens designed for the first yielding in both compression and tension flanges simultaneously. For the one-point loading condition, the test results indicated that for all sixteen panels, the ratios of the tested yield moment to the calculated effective yield moment using actual yield strength of the steel and the ratios of the tested ultimate moment to the calculated effective yield moment followed the similar trend with respect to the w/t ratio as the panels tested in two-point loading condition. In addition, for the one-point loading condition, the panels with small w/t ratios (17.93 to 31.65) developed higher ratios of the tested yield moment to the calculated effective yield moment and higher ratios of the tested ultimate moment to the calculated effective yield moment, but demonstrated less overall ductility in the load-displacement relationship as compared to the panels with the two-point loading condition. The panels with large w/t ratios (118.64 to 189.95) developed only slightly higher ratios of the tested ultimate moment to the calculated effective yield moment as compared to the panels with the two-point loading condition. For the deck panels with screws penetrating through tension flanges, it was found that the ultimate tested moment and displacement of the panels with screws were nearly equal to those of the panels without screws. Only one 22 gage panel with 27% of reduction in tension flange and designed for first yielding in tension flange experienced tensile fracture and necking near the holes after the panel entered a plateau in its load-displacement curve. The test results also showed that for almost all the deck panels with either a two-point or a one-point loading condition, the tested central displacements were near or less than the calculated central displacements using effective moment of inertia at service load, actual dimensions, and modulus of elasticity of 29,500 ksi. Fracture in tension was not observed in the tested panels without screws. The flexural strength of the panels was more strongly affected by the w/t ratios of the panels and did not appear to be influenced by the low-ductility and low Fu/Fy ratio of the steel for the panels with small w/t ratios. It is concluded that the current design practice for designing cold-formed flexural members using 75% of the specified minimum yield strength of the Structural Grade 80 of ASTM A653 steel or 60 ksi (whichever is less) is conservative, especially for the members with small w/t ratios (less than 60). A modified yield strength reduction factor was developed to be used for determining the flexural strength of the panels with yield strength between 80 ksi and 150 ksi (including 80 and 150 ksi) and w/t ratio not exceeding 190. For panels with (w/t)(Fy/E) ratio of 1/15 or less, the actual yield strength of steels can be used for determining the flexural strength of the panels. Reasonable agreements are achieved between tested moments and predicted moments using the modified yield strength reduction factor.
Department(s)
Civil, Architectural and Environmental Engineering
Sponsor(s)
American Iron and Steel Institute
Research Center/Lab(s)
Wei-Wen Yu Center for Cold-Formed Steel Structures
Appears In
Cold-Formed Steel Series
Publisher
Missouri University of Science and Technology
Publication Date
01 Nov 1996
Document Version
Final Version
Rights
© 1996 Missouri University of Science and Technology, All rights reserved.
Document Type
Technical Report
File Type
text
Language(s)
English
Recommended Citation
Wu, Shaojie; Yu, Wei-Wen; and LaBoube, Roger A., "Strength of flexural members using structural grade 80 of A653 steel (deck panel tests)" (1996). CCFSS Library (1939 - present). 49.
https://scholarsmine.mst.edu/ccfss-library/49
Comments
Second Progress Report